Cast and Cure Finds Niche for Many Applications
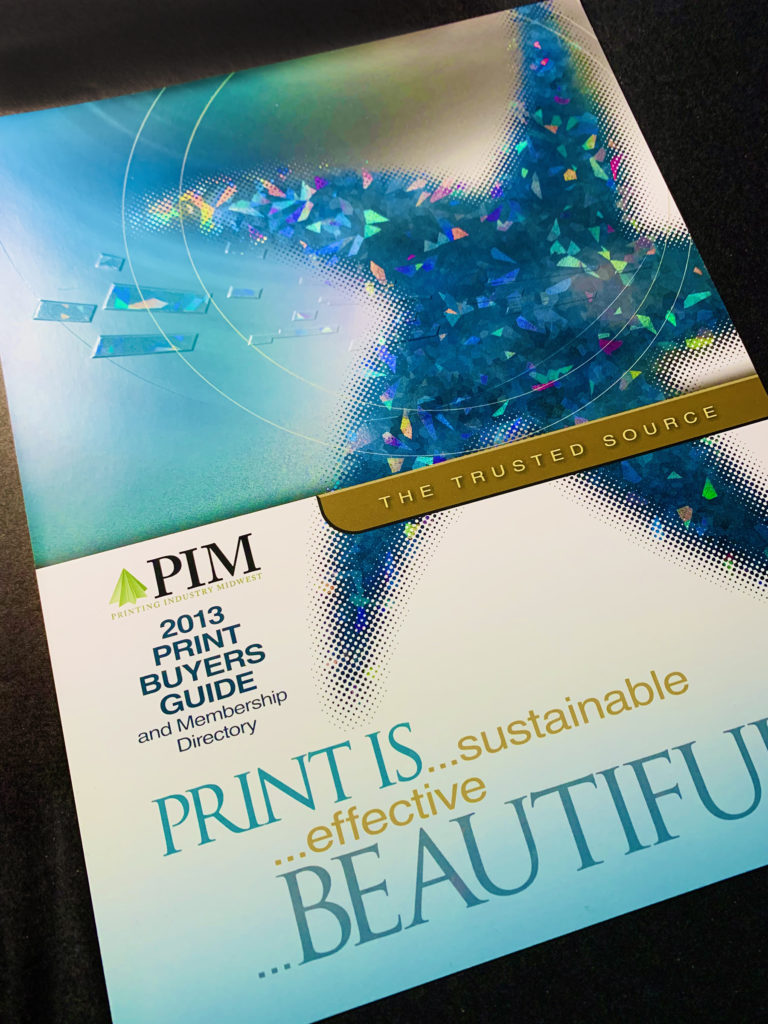
Originally published in PostPress Magazine, March 2022
Although film casting, known as Cast and Cure™, is not a new print technology, many industry veterans still misunderstand how the process actually works. PostPress sat down with Tim Cain, President of Breit Technologies, to discuss Cast and Cure™, the best applications, and the advantages and disadvantages of the process.
How does Cast and Cure work?
The Cast and Cure is a process in which you can create a decorative, clear holographic pattern on all types of printed substrates. First, a UV coating is applied to the substrate (labels, paper, paperboard, or flexible plastic). Then the casting film is nipped in contact with the wet varnish. UV light passes through the casting film and cures the varnish while the film holds the varnish in the desired shape, much like a mold. The film is then delaminated and separated from the printed web or sheet and is carefully re-wound so it can be used again. The Cast and Cure process leaves behind a beautifully micro-embossed shape in the coating’s surface that can be holographic, matte, or a texture.
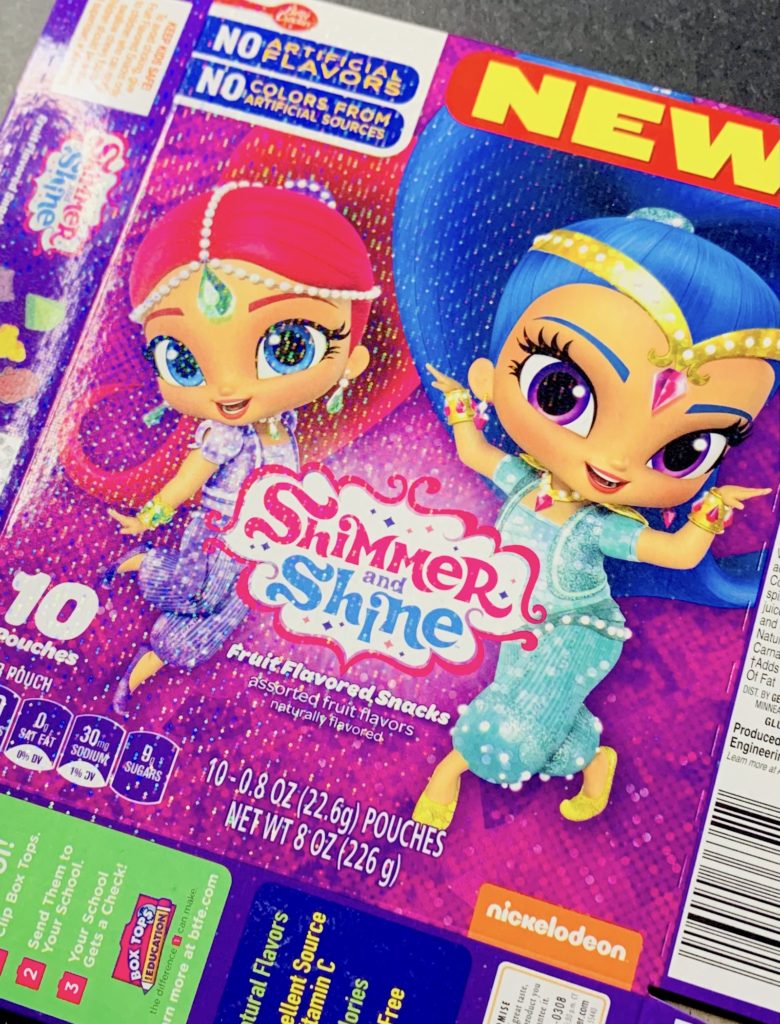
What are some of the most popular applications for Cast and Cure?
We see Cast and Cure used in everything from liquor and beverage labels, printed collateral and direct mail, magazine and book covers, and even food and pharmaceutical cartons. Brand owners find Cast and Cure clear holographic patterns are an excellent way to grab the consumer’s attention when it is applied to a carton or label. Since it is clear and transparent, the printed graphics and text is not affected and remains readable by the consumer.
What is the best way to design for Cast and Cure?
Designing for holography in general can be tricky. For instance, when a holographic metalized PET (H-MPET) substrate is used for a carton or label, it most commonly requires designing multiple opaque ink layers to mask those areas where the holography should not bleed through. Since Cast and Cure is applied over the UV varnish, masking specific areas is not needed. Rather, the designer can create a spot varnish layer on the artwork where they want it applied.
Although bold, solid color backgrounds showcase Cast and Cure holographic effects the best, it can also be used to create the illusion of movement over photographs and more busy backgrounds. Ultimately, however, there is no wrong way to use Cast and Cure holography or textured effects.
For most applications, Cast and Cure works best with a full coverage of the clear pattern over the printed image. It can be used in specific areas of a design, but full coverage provides the most impact and attention. In those cases, the designer needs to create a separate layer of solid black where the UV coating and casting film should be applied.
What are some of the benefits of this process?
As discussed earlier, the Cast and Cure micro-embossed film works as a type of mold for the cured UV coating; as such, the film is not actually applied to the substrate so can be reused up to a dozen times (and sometimes even more). This provides a significant cost savings in terms of the amount of film needed for any given job. There is less spent on shipping fees, warehousing, and waste disposal compared to other decorating methods, such as hot and cold foil. Moreover, since the film can be reused over and over, it is more sustainable than other processes.
What are the disadvantages?
Since Cast and Cure is applied to the surface of a UV coating, it reduces the effectiveness of any desired security features. Traditional security holograms are imbedded sub-surface to make it difficult to copy, so Cast and Cure is usually not used solely for security.
There are also limitations to the type of substrates it can be applied to. Since it’s applied to a coating of UV ink, a coated, smooth stock works best. An uncoated or textured stock will absorb the coating and not allow the process to work as well.
What can some of the on-press challenges be overcome?
The most common on-press challenge is poor tension control when winding the film back onto its roll. Once a wrinkle is introduced to the roll, it’s almost impossible to eliminate. Fortunately, if the press operator follows proper tension guidelines, they will be able to start and splice the film without wrinkles, ensuring that the film can be reused over and over again.
Applying the UV coating correctly before the casting film is introduced is also essential for the successful application of Cast and Cure.
Are there any new applications in the works?
Recently the shrink sleeve and gift-wrap market has started to embrace Cast and Cure, which is truly exciting. Brand owners with long-run jobs are also starting to use the technique, as the process can be applied now at close to 1,000 feet per minute.
We are also working to combine Cast and Cure with a monochrome inkjet system so a variable varnish application can be applied (such as unique security features, names, etc.) to individual printed pieces.